|
太阳能电池与组件 |
Solar Cell and module |
硅太阳能电池 |
硅太阳能电池采用硅晶体薄片制作,片厚约0.2mm,硅晶体薄片的尺寸一般为156mm×156mm(6英寸)或125mm×125mm(5英寸)。图1是单晶硅与多晶硅晶体薄片的照片(照片来自网络),左图是6英寸的单晶硅片,右图是5英寸的多晶硅片。 |
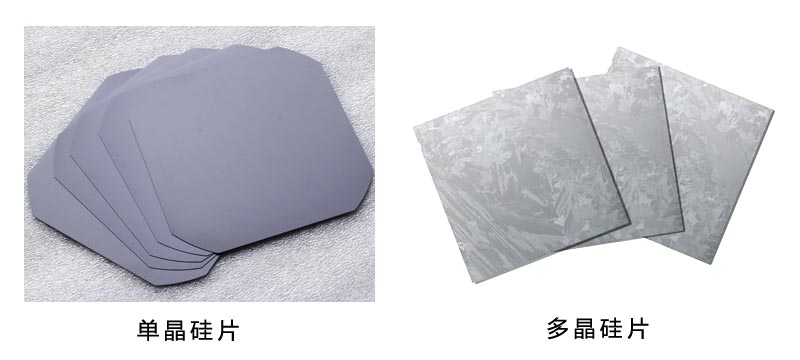 图1--单晶硅与多晶硅片(照片来自网络) |
在硅晶体薄片表面制作PN结,在上下表面做电极构成太阳能电池。图2是硅太阳能电池的结构示意图,该图显示的仅是硅太阳能电池的一小块截体。电池主体是PN结,为了防止硅晶体薄片对太阳光产生反射,把上表面制成无反射的绒面;为进一步减小反射,在上面还要敷一层透明的减反射膜;在电池上表面有电极线与N型半导体连接,在电池下表面有电极线与P型半导体连接。为了清晰显示层次,图中对N型半导体、绒面、减反射膜的厚度进行了放大,实际是很薄的。 |
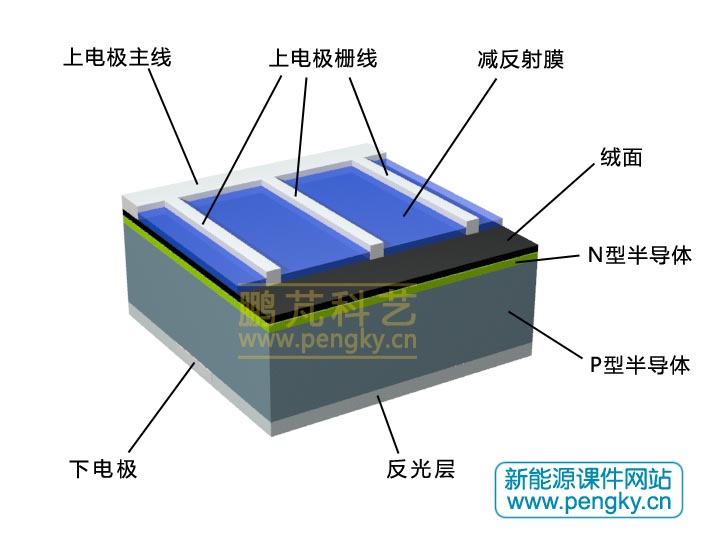 图2--硅太阳电池的结构示意图 |
制作太阳能电池的硅晶体为掺杂3价硼的P型半导体,主要制作流程是: 1. 抛光清洗
对硅片表面进行化学抛光并进行清洗。我们把朝向太阳的一面称为上表面,把背向太阳的一面称为下表面。 2. 制作绒面
光滑的硅晶体薄片表面会反射掉部分太阳光,见图3左图,为了防止对太阳光产生反射,要在薄片上表面用化学腐蚀生成凸凹面,凸凹面好像无数的金字塔排列在一起,使太阳光尽量射入硅晶体,见图3右图。只是这些金字塔非常细微,高约10μm,可使硅晶体薄片上表面反射大大减少,较全面的吸收太阳光。 |
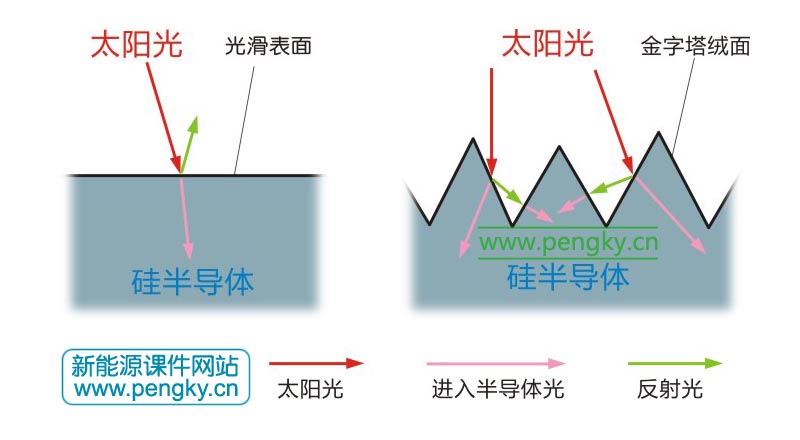 图3--金字塔绒面减少太阳光的反射 |
3. 扩散制结
在P型硅晶体薄片的绒面上表面扩散5价的磷,在绒面下生成0.3至0.5μm深的N型半导体,这样,在硅晶体薄片的上表面是N型半导体,在硅晶体薄片的下表面是P型半导体,交界面附近就是PN结,见图4。 4. 刻蚀去边
为防止上下表面短路,必须把硅晶体薄片周边因制结生成的扩散层去除。同时还要去除在硅片表面因扩散生成的磷硅玻璃与氧化物残迹。 5. 制作减反射膜
虽有绒面,但仍有经过二次或三次反射出去的太阳光,为进一步减少对光线的反射,还要在上表面沉积一层减反射薄膜,成分主要是和Si3N4(氮化硅)或TiO2(氧化钛),生成蓝色透明薄膜,膜厚为75nm至80nm,见图4。 |
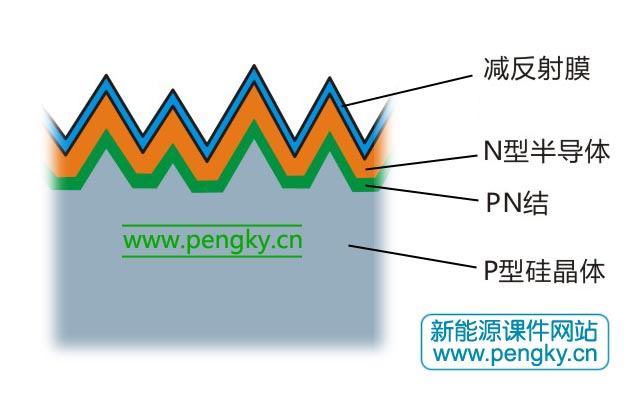 图4--硅太阳电池的上表面结构示意图 |
6. 制作上下电极
在上下表面制作连接外电路的电极,上电极要尽量减少对射入光线的遮挡,使用多根细线(栅线)把电流汇集到较粗的引出线(主线),上电极线主要采用银浆丝网印刷的方法制作。下电极用银铝浆丝网印刷宽的母线,然后再在整片上印一层铝浆做反射层,把穿透过来的光子反射回去。
为了使银、铝浆电极与硅材料完全紧密接触,还需通过烧结过程,烧结使双方材料表面的原子相互融入,特别是可以烧穿减反射膜,使上电极与硅半导体紧密接触。
下面是硅太阳能电池制作主要流程动画。 |
|
硅太阳能电池制作主要流程动画 |
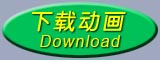 |
图5是单片单晶硅太阳能电池与多晶硅太阳能电池图片,电池片上横的细线是栅线,竖的粗线是主线。 |
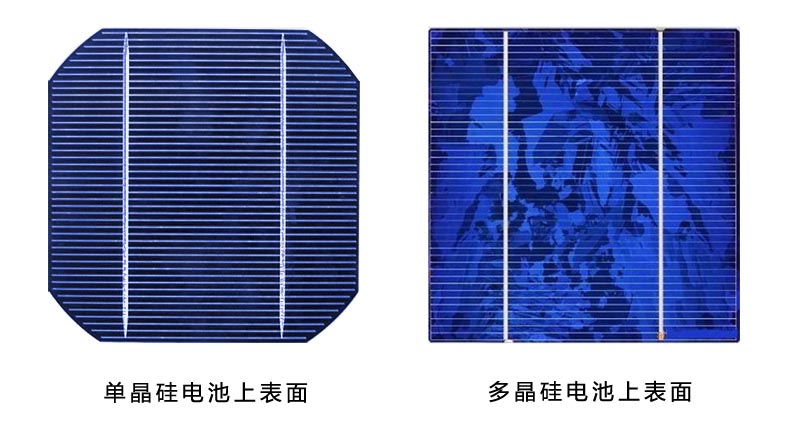 图5--硅太阳电池片(照片来自网络) |
太阳能电池的每一个生产环节都要进行严格的质量检查,不让有缺陷的产品进入下个生产环节,太阳能电池最后一个环节是电气性能性能检测,也就是通过测量得到太阳能电池的伏安特性曲线。要测量主要参数是开路电压、短路电流、最大功率点、最佳工作电压、最佳工作电流、转换效率等。最后根据外观与所测参数对电池进行分级分类。 |
太阳能电池组件 |
单个硅太阳能电池片的输出电压约0.4伏,必须把若干太阳能电池片经过串联后才能达到可供使用的电压,并联后才能输出较大的电流。多个太阳能电池片串并联进行封装保护可形成大面积的太阳电池组件,太阳电池组件是太阳能发电系统的基本组成单元。
图6是一块太阳能电池组件,也就是常说的太阳能电池板。 |
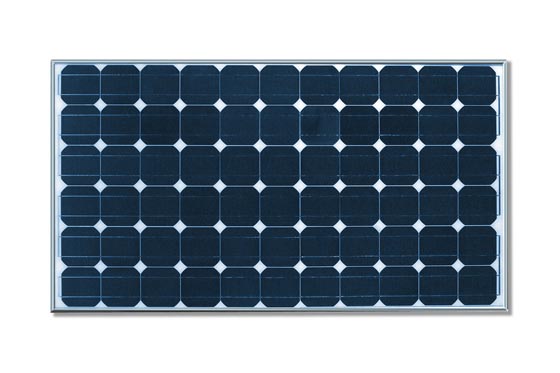 图6--太阳电池组件(照片来自网络) |
太阳电池组件的主要生产过程如下。
1. 电池分选
为提高电池片的利用率,将性能一致或相近的电池片组合在一起,应根据其性能参数进行分类;电池测试即通过测试电池片的输出参数(电流和电压)的大小对其进行分类。 2. 电池片的焊接
汇流带为镀锡的铜带,使用电烙铁和焊锡丝将汇流带焊接到电池上面(负极)的主线上,伸出的汇流带将与后面的电池片的背面电极相连。
通过背面焊接将N张片电池串接在一起形成一个电池串,称为串焊,使用电烙铁和焊锡丝将单片焊接好的电池的上面电极(负极)的伸出端焊接到下一个电池的下电极(正极)上,见图7上图,图7下图是以焊好的3个电池片。图7中各零件相互间的尺寸比例与实际有较大差别,仅为示意图。 |
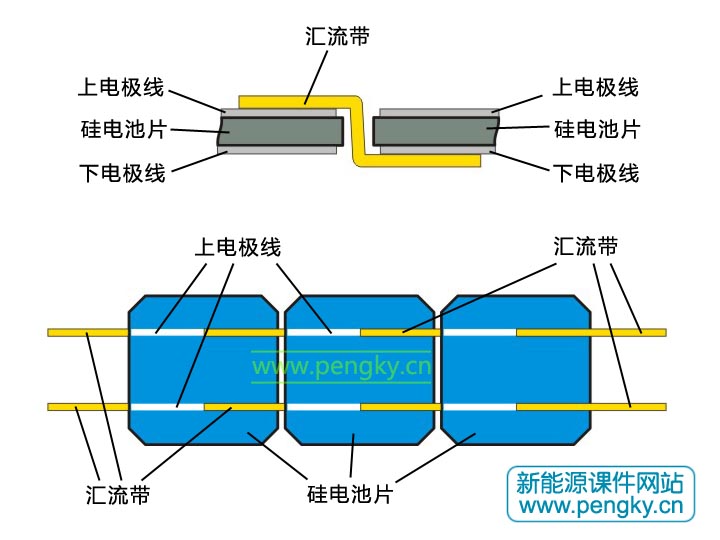 图7--电池片的焊接 |
将串接在一起的整个电池串的正负极焊接出引线,并检验整个电池串的特性,修理有问题的电池串。
3. 叠层
太阳能电池组件的种类较多,按照封装材料和工艺的不同与用途的不同,封装方式也不同,下面介绍的是普通硅太阳能电池的常用封装方式。
在电池串的上面采用钢化玻璃封装,有很高的强度与很好的透光性,可有效地保护电池片;电池片的下面采用有良好绝缘性能、能抗紫外线抗环境侵蚀的热塑聚氯乙烯复合膜(TPT)做背面:三者之间采用热融胶粘膜(EVA)进行粘接,EVA透光率高,并有柔韧、耐冲击、耐腐蚀,在热压下熔融固化后有很好的粘合性。封装的层次见图8. |
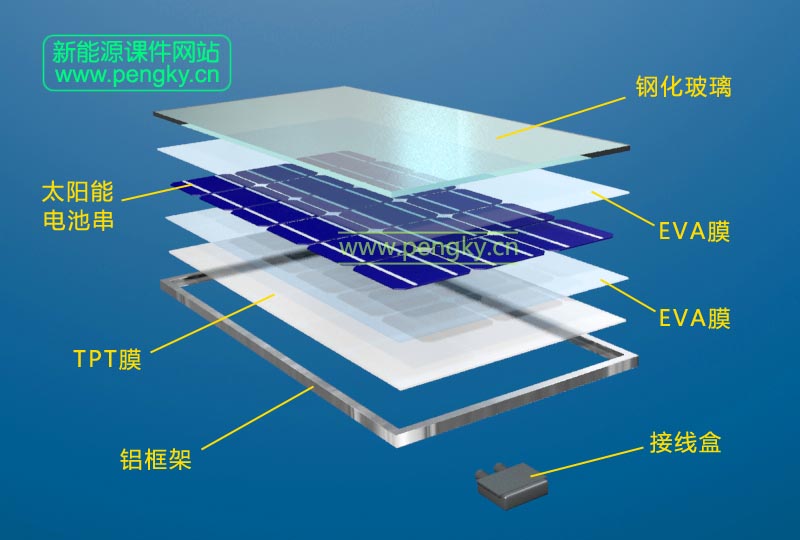 图8--太阳能电池组件叠层结构 |
将电池串、钢化玻璃和切割好的EVA 、TPT背板按照一定的层次敷设好,敷设时保证电池串与玻璃等材料的相对位置,调整好电池间的距离,准备层压。
4、组件层压
将敷设好的电池组件放入层压机内,通过抽真空将组件内的空气抽出,然后加热使EVA熔化将电池、玻璃和TPT背板粘接在一起;最后冷却取出组件。层压工艺是太阳能电池组件生产的关键一步,层压温度和层压时间根据EVA的性质决定。
层压时EVA熔化后由于压力而向外延伸固化形成毛边,所以层压完毕应将其切除。
7、装框
类似与给玻璃装一个镜框;给玻璃组件装铝框,增加组件的强度,进一步的密封电池组件,延长电池的使用寿命。边框和玻璃组件的缝隙用硅酮树脂填充,各边框间用角键连接。
在组件背面引线处粘接一个接线盒,以利于电池与其他设备或电池间的连接。
图9是封装好的单晶硅太阳能电池组件正面与反面,图10是封装好的多晶硅太阳能电池组件正面与反面,在反面可看到电池接线盒。 |
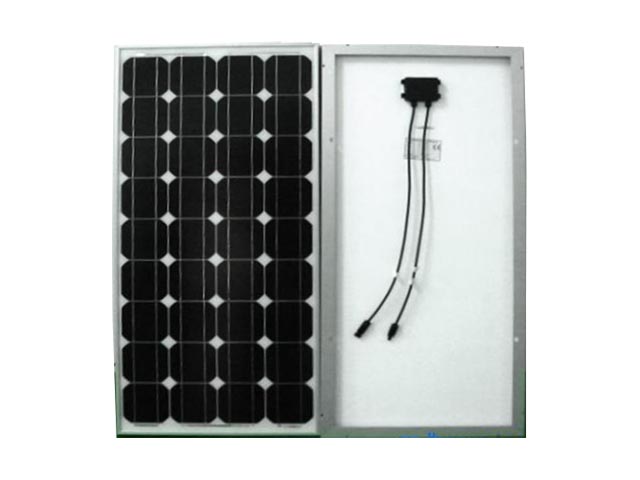 图9--单晶硅太阳能电池组件正面与反面(照片来自网络) |
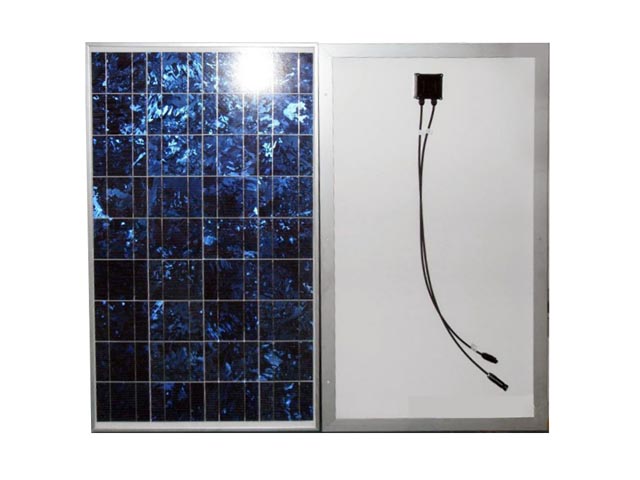 图10--多晶硅太阳能电池组件正面与反面(照片来自网络) |
太阳能电池组件也就是常说的太阳能电池板,作为太阳能发电场用的尺寸较大,大的可达2米长1米宽,一般为1.5m长,0.8m左右。也可根据需要做成不同尺寸、不同电压、不同形状的组件,见图11。 |
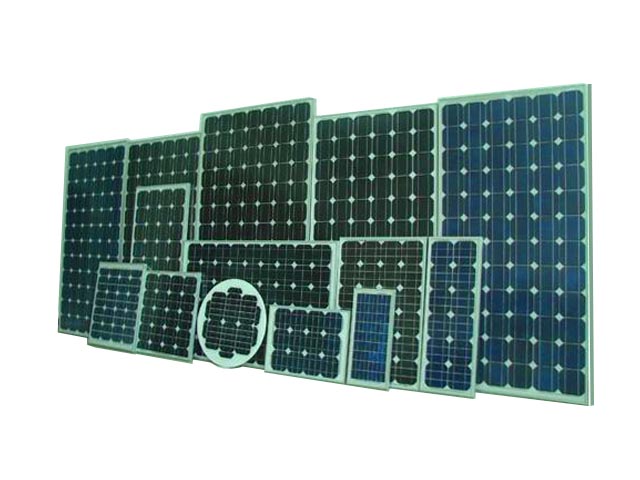 图11--多种尺寸的太阳能电池组件(照片来自网络) |
8、组件测试
测试的目的是对电池的输出功率进行标定,测试其输出特性,确定组件的质量等级。在标准光照条件(辐照度1000W/m²)下的输出电压一般为30至50伏,短路电流约10安培。
在实际应用中,若干电池组件安装在同一个支架上,串并连接后输出,通常把这些组合在一起的太阳能电池称为太阳能电池阵列(方阵)。
图12是太阳能电池与太阳能电池组件的图形符号,符号是普通电池符号加个圆圈,极性与普通电池一样,图12下方是太阳能电池组件或阵列的常用画法。
|
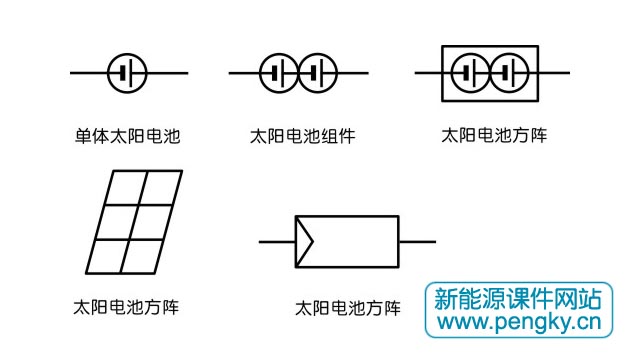 图12--太阳电池与组件的图形符号 |
|